
Typically, the motor control center has panel meters that indicate the temperatures sensed by the detectors. Motors equipped with temperature detectors embedded in the windings are usually monitored by directly reading the output of the detectors with appropriate instrumentation. Further, if the ambient temperature at the motor installation were to go above 25 C, the motor load would have to be reduced to avoid exceeding the machine’s total temperature (hot winding) capability.ĭetermine temperature rise using detectors Although that is acceptable, it is important to keep in mind that any increase in load will result in excessive temperature rise and serious thermal degradation of the motor’s insulation system. Notice that the calculated temperature rise of 104 C in the example is just 1 deg below the limit for Class F (105 C) in Table 1. The temperature rise equals the hot winding temperature minus the ambient temperature, or in this case: Plug the cold and hot resistance measurements into the following equation to find the hot temperature then subtract the ambient temperature from the hot temperature to obtain the temperature rise.Įxample: An unencapsulated, open drip-proof medium motor with a Class F winding and a 1.0 service factor has a lead-to-lead resistance of 1.02 ohms at an ambient temperature of 25 C, and a hot resistance of 1.43 ohms. Then run the motor at rated load long enough for the temperature to stabilize (up to 8 hours sometimes) and measure the hot resistance in the same way. Be sure to record the ambient temperature as well. To find the temperature rise using the resistance method, measure the lead-to-lead resistance of the line leads with the motor cold-i.e., at room (ambient) temperature.
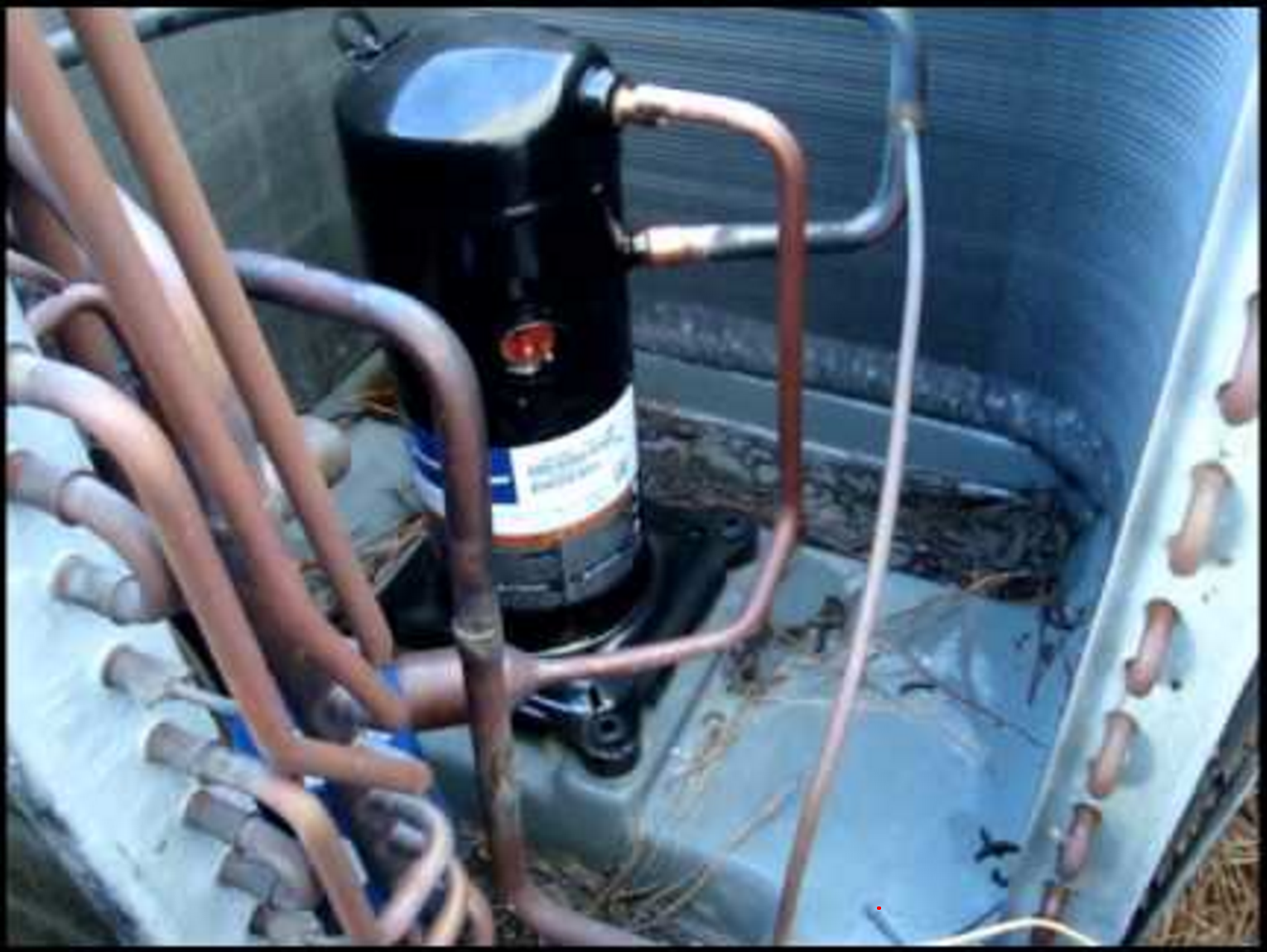
The temperature rise of large motors can be measured by the resistance method or by detectors embedded in the windings as indicated in Tables 2 and 3. Note that temperature rise limits for medium motors in Table 1 are based on resistance. The resistance method is useful for determining the temperature rise of motors that do not have embedded detectors-e.g., thermocouples or resistance temperature detectors (RTDs). Table 2 lists the temperature rise for motors with a 1.0 SF Table 3 applies to motors with 1.15 SF. Temperature rise limits for large motors-i.e., those above medium motor ratings-differ based on the service factor (SF). In the most common speed ratings, the NEMA designation of medium motors includes ratings of 1/2–500 hp for 2- and 4-pole machines, and up to 350 hp for 6-pole machines. Table 1 shows the temperature rise limits for NEMA medium electric motors based on a maximum ambient temperature of 40 C. But NEMA also builds in a safety factor, primarily to account for hot spots-i.e., parts of the motor winding that may be hotter than the location at which the temperature is measured. Since the maximum ambient temperature according to NEMA MG 1-2003 is normally 40 C, one would expect the temperature rise limit for a Class B system to be 90 C (130 C – 40 C). For example, a Class B insulation system is rated 130 C, while a Class F system is rated 180 C.
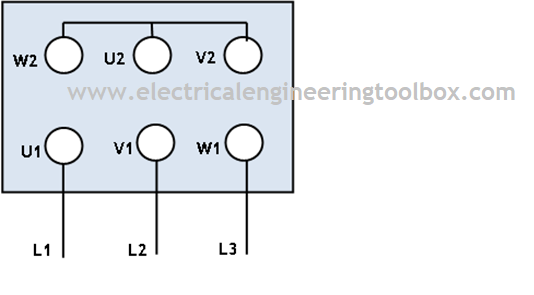
NEMA rates insulation according to its ability to withstand overall temperature. The difference between the ambient temperature and that of a motor operating under load is the temperature rise (temperature rise = hot temperature – ambient temperature).
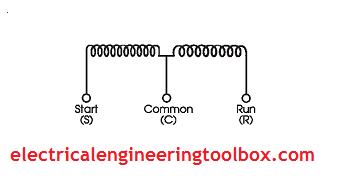
Once the temperature rating is known, the temperature rise can be measured directly using sensors or an infrared temperature detector, or indirectly using the resistance method.Īmbient temperature is the temperature of the air (or other cooling medium) that surrounds the motor.
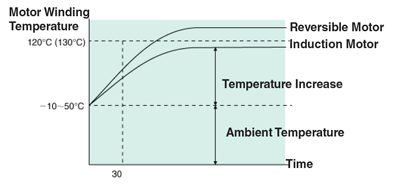
Temperature rating also can be found on the motor’s original nameplate. The National Electrical Manufacturers Association (NEMA) defines this rating for three-phase induction motors in its standard Motors and Generators, MG 1-2003. The first step to prevent unexpected shutdowns and extend motor life is to determine the temperature rating of the motor. But it is easy to forget that exceeding the rated operating temperature by as little as 10 C (18 F) can shorten the life of a three-phase induction motor by half. It is no secret that heat kills electric motors. Regularly checking the operating temperature of each critical motor will pay dividends.
